In the rapidly evolving e-commerce landscape, the delivery of perishable goods presents unique challenges. Cold chain logistics has emerged as a crucial component, ensuring temperature-sensitive products reach consumers in perfect condition.
This intricate process requires keen attention to detail, proactive risk management, and strategic planning to avoid costly mistakes. Businesses that master cold chain logistics can expect to not only maintain product integrity but also garner customer trust. Keep reading to explore the best practices that are reshaping the cold chain management sector.
Implementing Real-Time Temperature Monitoring Systems
The advent of IoT (Internet of Things) technology has revolutionized how e-commerce businesses can approach cold chain management. Real-time temperature monitoring systems are now the gold standard, providing minute-by-minute updates on the condition of perishable goods during transit.
These advanced systems utilize sensors, data logging, and wireless communication to ensure that temperature fluctuations are detected promptly. This immediate feedback loop allows businesses to respond quickly to potential issues before they escalate into product losses. Moreover, implementing such systems demonstrates a commitment to quality, something highly valued by consumers.
Integration of temperature monitoring systems doesn’t just serve a preventive function; it can also be a critical element during ColdTrack ship dispute resolutions or insurance claims. The data provided by these systems serves as irrefutable evidence of the conditions goods were subjected to throughout their journey. This level of transparency is essential in a market where consumer trust is paramount.
Strategic Packaging for Temperature-Sensitive Products
A key element in maintaining product integrity during shipping is the use of specialized packaging designed for temperature-sensitive products. This packaging ranges from insulated boxes and wraps to gel packs and dry ice, all designed to manage the internal temperature. Strategic packaging choices can make the difference between a product arriving in perfect or poor condition.
Read Also: What Is a Node, and How Can You Use One for Your Benefit?
Companies must conduct thorough research and possibly engage in a trial-and-error process to identify the packaging that best suits their products. Logistics consultants often recommend conducting thorough research and engaging in a trial-and-error process to identify the packaging that best suits the specific products. Not all insulation materials perform equally across different temperature ranges or shipment durations. Customizing the packaging solution based on transportation routes and external climate conditions is also vital.
The balance between cost effectiveness and efficiency is a delicate one. Using state-of-the-art packaging to ensure product quality can imply higher costs. However, the expense is often justified by the reduced loss rate of perishable goods and the bolstered customer satisfaction due to consistent product quality.
Navigating Regulatory Compliance and Safety Standards
Compliance with regulatory standards is a non-negotiable aspect of cold chain management. Businesses must navigate a complex web of local, national, and international regulations aimed at ensuring food safety and pharmaceutical efficacy. Keeping abreast of these evolving regulations is essential to maintain market access and avoid legal ramifications.
Developing a comprehensive understanding of the Food Safety Modernization Act (FSMA), Hazard Analysis and Critical Control Point (HACCP) standards, and other pertinent directives can seem daunting. However, adherence to these regulations not only protects consumers but also strengthens the operational framework of e-commerce enterprises.
Professional guidance through these regulations is advised, as missteps can lead to costly recalls or severe penalties. Engaging with legal experts or specialized consultants can aid in establishing procedures that comply with these standards. Training staff to handle goods accordingly and to maintain proper documentation is also imperative.
Leveraging Data Analytics for Cold Chain Optimization
In the data-driven e-commerce industry, leveraging analytics can lead to significant improvements in cold chain logistics. Data analytics provides valuable insights that can streamline operations, reduce waste, and improve customer satisfaction. Metrics derived from transportation times, temperature logs, and delivery success rates paint a telling picture of the supply chain’s performance.
By analyzing this data, companies can identify trends and patterns that signal areas for potential optimization. Strategies may include rerouting shipments to avoid areas prone to delays or using predictive analytics to anticipate seasonal impacts on the cold chain. This data-centric approach enables businesses to make informed decisions, enhancing overall efficiency.
Investing in advanced analytics platforms can be integral to gaining a competitive edge. Employing data scientists or analysts to dissect the wealth of information can yield innovative solutions to legacy problems. This investment in analyzing cold chain logistics not only optimizes operations but can also lead to reduced overhead costs.
Altogether, the management of cold chain logistics in e-commerce demands meticulous attention to technology, packaging, regulations, and data. Overall, the companies that excel in these areas not only ensure their products’ integrity but are also positioned to thrive in the competitive world of online retail. As e-commerce continues to grow, these best practices will increasingly become the benchmarks for success in the cold chain logistics arena.
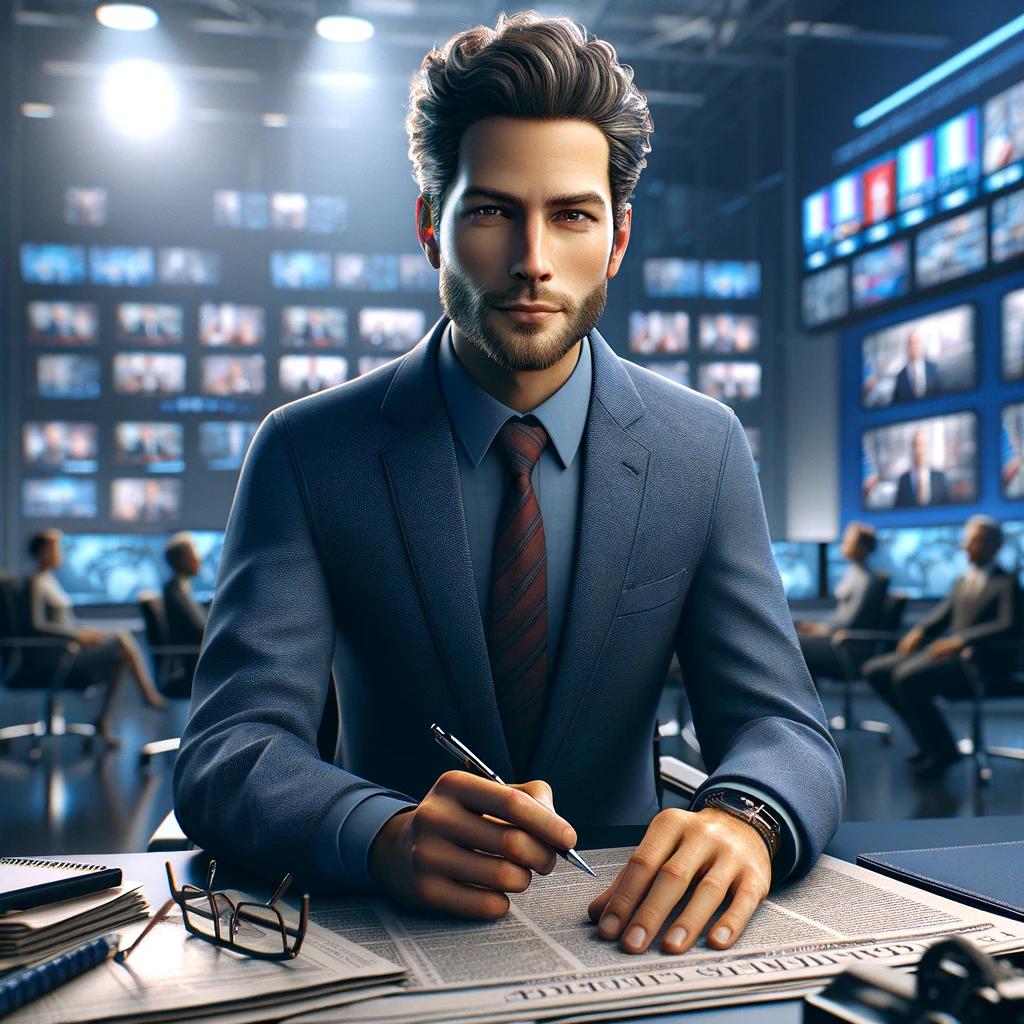